At Forcys, we understand that modern maritime security demands more than just sophisticated sensors or autonomous vehicles – it requires seamless integration of cutting-edge technology. This is where the combined expertise of our technology partners comes into play. The capabilities of EIVA’s ViperFish, alongside advanced solutions from Sonardyne, and Wavefront Systems are reshaping how subsea threats are monitored and managed, ensuring that the maritime defence community has the tools needed for effective real-time operations.
ViperFish is an all-in-one remotely operated towed vehicle (ROTV) designed for high-resolution data collection in autonomous operations. At Forcys we see the integration of this product as a significant step forward in autonomous operations. Designed for seabed imaging and geophysical surveys, ViperFish performs these tasks with remarkable precision, particularly and can even be paired with unmanned surface vessels (USVs). This opens up new possibilities for autonomous operations in complex underwater environments, enhancing mission safety, efficiency and data accuracy.
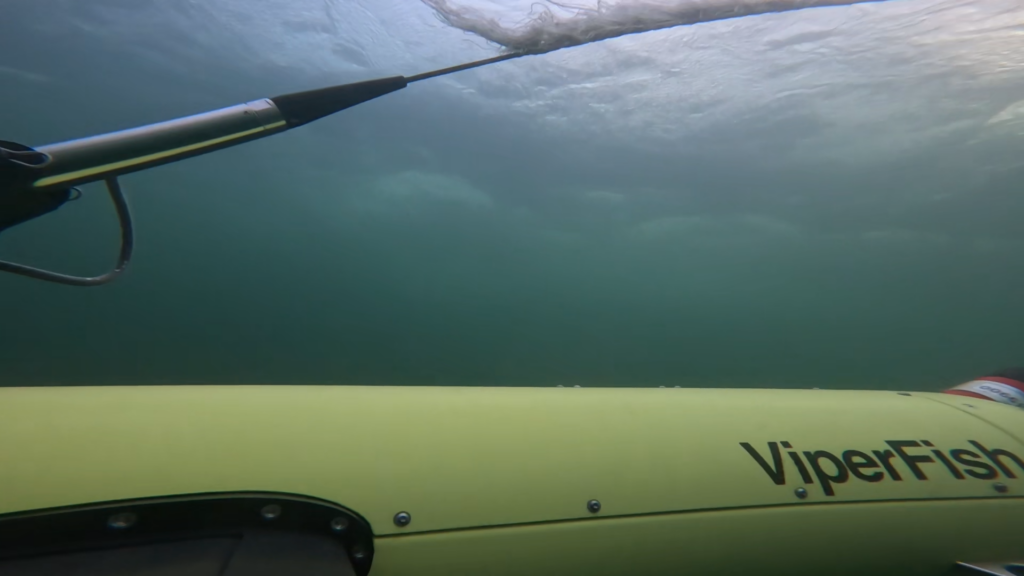
By combining this ROTV with positioning systems, sonar technology and EIVA’s NaviSuite survey software, we deliver a powerful, integrated solution that supports critical defence missions. ViperFish’s ability to automatically maintain a set height above the seabed makes it an invaluable tool for mine countermeasures, UXO (unexploded ordnance) surveys, and rapid environmental assessments.
“Forcys leverages Covelya Group partnerships to deliver solutions that provide capabilities beyond the sum of their individual components,” says Antonio Belfiore, Senior Sales Manager at Forcys. “Additionally, the combined research and development expertise across our group of companies enables Forcys to rapidly adapt to emerging threats and evolving mission requirements. This knowhow was instrumental in the development of ViperFish. Designed to be the tool of choice for mine-hunting across the littoral and in riverine environments, Viperfish is also easy to use and provides your team actionable data in real-time.”
In the context of mine warfare, these integrated solutions are revolutionising the way threat detection is carried out. By relying on autonomous vehicles that can navigate complex underwater environments with precision, defence teams can carry out missions more efficiently and frequently than ever before. The combination of ViperFish’s flexibility and the advanced sensor technologies it brings together enables vast subsea areas to be covered with unprecedented detail.
These advancements not only improve operational efficiency but also provide the necessary foundation for many future maritime and defence security operations.
At Forcys we’re proud to be part of this journey, ensuring that autonomous technology plays a central role in securing your assets.
Read more about our technology partner EIVA.
Discover ViperFish ROTV deployed by ProZero 8m Naval Intelligence USV:
The ViperFish is an all-in-one compact remotely operated towed vehicle (ROTV) ideally suited for expeditionary mine countermeasures (MCM) and explosive ordnance disposal (EOD) surveys. Martin Kristensen, VP of Hardware Development at our technology partner EIVA, explains all in this edition of The Watch.
“The ViperFish is a new surveying platform that we developed to address the growing demand for unexploded ordnance (UXO) surveying in the offshore wind industry,” said Kristensen. “It is a versatile and easy-to-use system that can be deployed from a vessel of opportunity. Expeditionary MCM survey requirements are very similar so navies can benefit from all our commercial experience to make their surveys far more efficient.”
Experience where it counts
“We wanted to incorporate all the lessons we learned from building and operating the ScanFish ROTV, the industry’s leading UXO survey platform, into the design of the ViperFish, creating a UXO surveying platform optimised to meet the demands of our customers. These include increasingly efficient surveys and where possible these needed to be automated. To support an increasing volume of surveys, new ROTVs needed to be compact, easy to launch and recover from a variety of vessels, including uncrewed surface vessels (USVs), and equipped with class-leading payloads and navigation sensors.
The system is built using the same building blocks as the ScanFish, enabling us to leverage all that experience. The first obvious difference between the ViperFish and the ScanFish is the shape. The ViperFish is cylindrical with actuated fins, while the ScanFish is shaped like an airfoil. The new system is as manoeuvrable, but the difference in shape offers a number of benefits:
- A lower drag coefficient: this means that it requires less power to tow. This is important for autonomous UXO surveys, as it allows the ViperFish to be deployed from smaller vessels or even from shore.
- More stability in rough seas: the pitch and roll are controlled by the actuators maintaining a more stable platform enabling you to work closer to the seafloor and maintain a stable platform at the sweet spot for the sensors providing improved data and therefore better decision making.
- A narrower profile enabling operations from smaller vessels: making it easier to transport and deploy. This is a major advantage for expeditionary surveys, as it allows the ViperFish to be deployed and recovered more quickly and easily.
It’s not just the platform. It’s the whole system. We conducted significant research to minimise the cable drag. By doing this, we can operate with smaller winches and deploy from a smaller surface area. We offer two shipment options: a self-contained cradle-box that can be shipped everywhere, or a container ready to integrate into a vessel.
It’s taken some time, but one of the most memorable things about the ViperFish is the first time we put it in the water,” said Kristensen. “On our first prototype test, we were out sailing 3 days and we had 100% uptime on the system. It was really a relief and a joy to see that all of our hard work had paid off.”
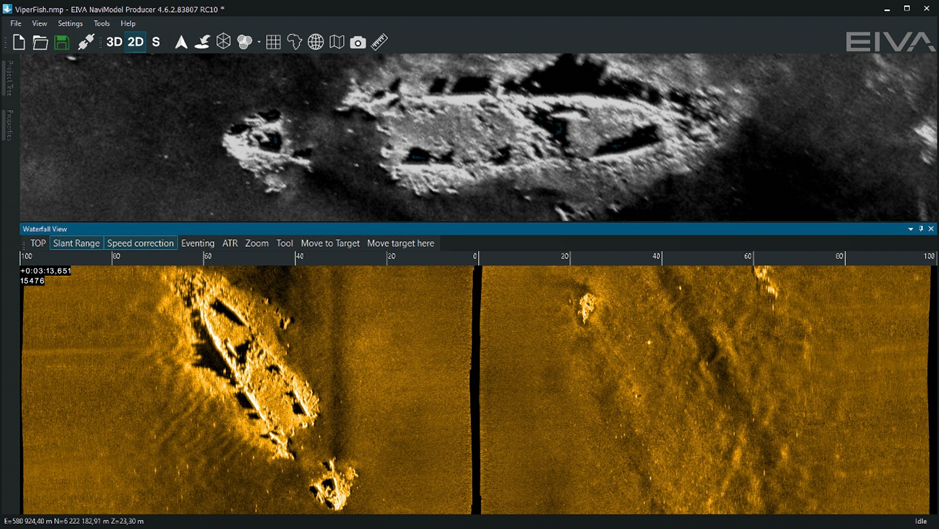
All the payloads
The ViperFish is equipped with all the sensors typically required on an ROTV, including:
- Solstice multi-aperture sonar: Used to create a two-dimensional image of the seabed. This image can be used to detect mine-like objects. The ViperFish uses the Solstice from our technology partner Wavefront Systems. This sonar is known for its high resolution and low power consumption.
- R2Sonic 2020 multibeam echosounder: It creates a three-dimensional image of the seabed. This is used to fill the gap ensuring 100 % coverage from a single survey line.
- OFG Hypermag: This magnetometer detects magnetic anomalies in the water or on the seabed generated by mines or other metallic objects while filtering out magnetic anomalies generated by the ViperFish itself.
- SPRINT-Nav Mini hybrid DVL-INS: Used to track orientation, position and speed; this system is from our technology partner Sonardyne. This information is used to create accurate maps of the survey area.
- Mini-Ranger 2 USBL positioning: The ultra-short baseline positioning system is used to track the ViperFish’s position in absolute coordinates. The Mini-Ranger 2 is a class-leading positioning system from our technology partner Sonardyne.
- Valeport sound velocity sensor: the sensor is used to optimise the sonar survey in real time, which is especially important when operating close inshore and within estuaries where sonar conditions can change rapidly.
The integration of these sensors into the ViperFish ROTV makes it a versatile and efficient UXO surveying platform. The ViperFish can be used to conduct surveys in a variety of conditions, and it can detect a wide range of objects.
Low-logistics, simple to operate, quick to train
“The ViperFish is operated by a crew of two people. The survey plans are prepared beforehand using NaviSuite Kuda software from EIVA. When launching the system, one person is responsible for supervising the ViperFish, while the other person controls the crane. At a speed through water of 2 to 10 knots, once in the water the ViperFish automatic controls take over, quickly swimming to the appropriate height from the seafloor within less than a minute. When the system is deployed one person is responsible for monitoring the automated mission while operating the ViperFish’s sensors and collecting data. If the ViperFish detects a possible UXO, the crew can mark the location on a map. The crew can then return to the location at a later time to investigate further. The system follows the seabed at a fixed height and can cope with slopes of up to 45 degrees. Plus it can replan its mission if obstacles are detected and avoid them in a safe manner while still obtaining high-quality data. When the mission is completed, the ViperFish is recovered by the two-person crew. We are also in discussions with USV manufacturers to make the launch and recovery totally automated.”
“The system is relatively easy to operate, even for people who are not trained hydrographers. The whole training process can be completed in a couple of weeks, it is mostly focused on learning how to set up the system and how to operate the sensors. If the crew is already experienced with using autonomous underwater vehicle (AUV) systems or the ScanFish, the training process will be a couple of days at most. Since the user interface of NaviSuite Kuda, EIVA’s survey software, is used widely in the commercial sector, there is already a large pool of contractors and trainers ready to support operations. In addition, sailors will be gaining valuable skills to support their transition to the commercial sector.”
Actionable data
“Ultimately, it’s about delivering our customers the best data, and you’ll be surprised how challenging it is to get these many payloads into the right form factor. But it has been worth it. We offer an incredible amount of area coverage rate of actual actionable data using class leading sensors.”
Please contact us to find out more.
If you have to operate side-scan sonars and synthetic aperture sonars (SAS) in very shallow waters (VSW) or shallow waters (SW), the acoustic environment is particularly hostile. Higher order multi-path reverberation, unstable velocity of sound profiles, often unknown, as well as significant bathymetry, baseline decorrelation effects and generally far fewer stable platforms, all add up. The result is far less reliable end sonar products with greater impact to longer range systems. This is particularly acute in tidal and riverine environments. What to do?
Go back to the drawing board
When Solstice was developed in 2010, our technology partner Wavefront Systems decided it was time for a step up in the performance of traditional side-scan sonars. The aim was to deliver a high-frequency, high-resolution, and long-range sonar that would provide a marked improvement in the probability of detection of mine-like objects while minimising the probability of false alarms.
Solstice was designed to do just that. Step one was to design a multi-aperture array which would improve the signal-to-noise ratio extending the range over other sonars operating at the same frequency. However, longer ranges in shallow waters are susceptible to multi-path reverberation. Dr Rob Crook, Research Director at Wavefront Systems explains how Solstice overcomes this problem: “The dominant source of noise for all side-scan sonars operating in shallow waters is ‘multi-path’ reverberation. The nature of this noise means many acoustic pathways scattering from spatially unrelated regions of the underwater scene may none-the-less return to the sensor with identical flight-times. The inability of any ‘2D’ (range, bearing) sensor to discriminate between these contemporaneous pathways leads to an inevitable loss of contrast. Multi-path Suppression Array Technology (MSAT) is a physical array-based technology that offers the swathe coverage one would traditionally have associated with wide elevation beam-widths, with the shadow contrast associated with very narrow beams. MSAT allows high shadow contrast right out to the maximum range of the sensor whilst maintaining high quality imagery close to nadir.” Why is contrast important? It helps to differentiate targets from the surroundings.
In addition, Solstice implements dynamic focusing ensuring that the image will maintain the highest possible resolution at the position in space relative to the sensor, meaning that the resolution will improve as the range to the target decreases. While at longer ranges the interpolated real-time imagery drastically aids human visual perception.
What does it all mean?
The design choices lead to significant advantages for Solstice users. These are some examples of where Solstice excels.
- Simpler to operate: Solstice is simple, the area coverage rate increases with speed while the range remains constant. This makes mission planning easy. You can understand and use the constant range to plot a survey route and you can observe the area that is under consideration. The survey outcome becomes more predictable and simpler to manage.
- More robust: Systems like SAS are known to be very sensitive when mounted on an unstable platform or operating over complex seafloor environments. Any dynamic changes may impact the quality of the SAS data; mud sediments can result in complete loss of micro-navigation data, and in the worst outcome the SAS needs to revert to normal side-scan mode. SAS typically operates at a lower frequencies hence this corrupted SAS side-scan data is not suitable for most operations. Solstice MAS does not share this problem.
- High currents: In MAS the range is limited as a function of the so-called ‘crabbing angle’ but the image quality is preserved along the whole swath.
- Shallow waters: Operations in confined spaces and shallow waters (20m to 30 m depth) are difficult for SAS systems or lower frequency side-scans. These systems can become range limited as the multipath effects from surface returns has an impact on the SNR performance and this is common for all side-scan sonars. For some SAS systems, these effects can compromise as much as 50% of their swath but with Solstice MAS, the impact will typically be less than 10%.
![]() | ![]() | ![]() | ![]() |
22 m | 47 m | 72 m | 92 m |
Please contact us to find out more.